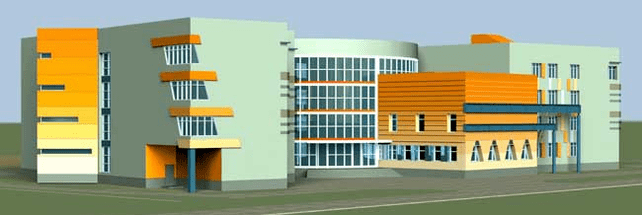
Energieeinsparung im Unternehmen - die Hauptrichtungen:
- Strom sparen
- Reduzierung von Wärme- und Dampfverlusten
- Reduzierung von Verlusten in Dampfleitungen
Energiesparen im Unternehmen - Energiesparmethoden
- Auswahl der optimalen Preiskategorie und Überarbeitung der Vertragsbedingungen der Stromversorgung
- Optimierung von Elektromotoren
- VFD-Installation
- Optimierung von Druckluftsystemen
Auswahl der optimalen Preiskategorie für die Stromversorgung
Insgesamt gibt es 6 Strompreiskategorien, nach denen Unternehmen Strom von garantierten Anbietern beziehen können.
In die erste Preiskategorie fallen alle Kleinunternehmen mit einer installierten Leistung von weniger als 670 kW zum Zeitpunkt des Vertragsabschlusses für eine automatische Stromversorgung.
Alle Unternehmen mit einer installierten Leistung von mehr als 670 kW fallen automatisch in die dritte Preiskategorie.
Die erste und dritte Preiskategorie sind nicht immer die optimalsten und günstigsten Netzteilkategorien.
In einigen Fällen kann der Wechsel in eine andere Preiskategorie die Stromkosten um 5 bis 30 % senken.
Das Thema Preiskategorien ist recht umfangreich, in unserem Test zu Preiskategorien erklären wir ausführlich, wie man die Preiskategorie des Netzteils richtig berechnet und auswählt.
Neben den Preiskategorien empfehlen wir auch, weitere Aspekte des Stromliefervertrages genau zu betrachten:
- Spannungspegel,
- Leistung,
- Stromübertragungstarif.
In unserem Testbericht erfahren Sie mehr über diese und weitere Methoden zur Senkung der Energiekosten.
Energiesparen im Unternehmen - Elektromotoren
Es ist notwendig, alle Geräte zu berücksichtigen, bei denen Elektromotoren verwendet werden:
- Pumps,
- Kompressoren,
- Fans,
- Werkzeugmaschinen,
- Fertigungslinien.
Steuerungsplan für Elektromotoren
Der Motorkontrollplan sollte ein integraler Bestandteil des Energiesparprogramms der Anlage werden.
Ein solcher Plan wird dazu beitragen, ein langfristiges Energiesparsystem für alle Elektromotoren im Unternehmen zu implementieren.
Der Motorsteuerungsplan stellt sicher, dass Ausfälle und Störungen nicht auftreten und wenn doch, schnell und effizient behoben werden.
Schritte zum Erstellen eines Motorsteuerungsplans:
- Führen Sie eine Bestandsaufnahme aller Motoren in der Anlage durch.
- Erstellen Sie eine Liste von Motoren mit ihren wichtigsten Parametern, technischem Zustand und Lebensdauer.
- Allgemeine Anweisungen zur Durchführung von Reparaturen erarbeiten.
- Entwickeln Sie Richtlinien für vorbeugende Wartung, Schmierung und Inspektion.
- Erstellen Sie einen Sicherheitsbestand an häufig verwendeten Ersatzteilen.
- Erstellen Sie eine Kaufspezifikation für neue Motoren.
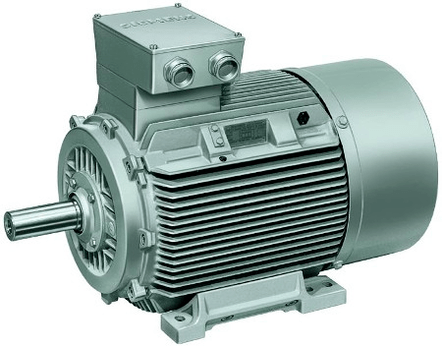
Aufwickeln von Elektromotoren
Generell ist das Aufwickeln eines alten Elektromotors viel günstiger als der Kauf eines neuen.
Der Elektromotor sollte ersetzt werden, wenn die Kosten für das Aufwickeln mehr als 60 % der Kosten für einen neuen betragen.
Dann hängt alles davon ab, wie das Zurückspulen durchgeführt wird.
Wenn die Arbeit auf höchstem Niveau verrichtet wird, verliert der Motor nur 1% -2% seiner Effizienz.
Wenn das Zurückspulen schlecht durchgeführt wird, erhöhen sich die Verluste im Elektromotor um 5% -10%.
Der Austausch des alten Elektromotors durch einen neuen energieeffizienten ist sinnvoll, wenn der Motor mehr als 2000 Stunden pro Jahr läuft.
Die Amortisationszeit für einen neuen energieeffizienten Motor beträgt nicht mehr als 1, 5 - 2 Jahre.
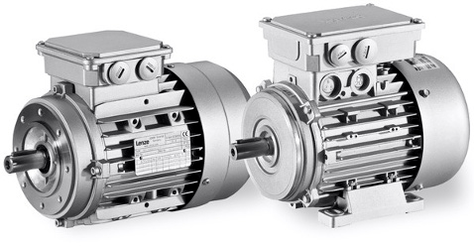
Energieeinsparung im Betrieb durch Erhöhung des Auslastungsgrades
Der Lastfaktor ist das Verhältnis von Betriebsleistung zu Scheinleistung.
So wird Energie effizient genutzt.
Je höher der Lastfaktor, desto effizienter wird der Strom genutzt.
Der Elektromotor arbeitet optimal ab 75 % Last.
Daher ist die Installation von Motoren oberhalb der erforderlichen Leistung (aus Sicherheitsgründen) nicht nur teurer, sondern auch in Bezug auf den Energieverbrauch ineffizient.
Der Lastfaktor kann wie folgt erhöht werden:
- Abschalten von unbelasteten Motoren,
- Austausch von Motoren, die weniger als 45% belastet sind, gegen leistungsschwächere Modelle,
- Umverteilung der Last zwischen den vorhandenen Elektromotoren.
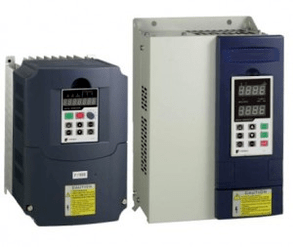
Frequenzumrichter (VFD)
Der Einbau von Frequenzumrichtern ist nur bei dynamischen Systemen sinnvoll.
Bei statischen Anlagen, die beispielsweise nur zum Heben von Lasten eingesetzt werden, hilft der Einbau eines Frequenzumrichters nicht und kann oft schaden.
Der VFD gleicht Last und Drehzahl des Motors aus und stellt so sicher, dass die elektrische Leistung optimal genutzt wird.
Der VFD kann den Energieverbrauch des Motors um mindestens 5 % und maximal 60 % reduzieren.
Die Amortisationszeit für VFD beträgt in der Regel 1-3 Jahre.
Optimierung von Druckluftsystemen
Druckluft wird in den unterschiedlichsten Branchen eingesetzt.
In einigen Unternehmen ist Druckluft der Hauptverbraucher von Strom.
Druckluft wird in pneumatischen Geräten und Ausrüstungen, auf Förderbändern, automatischen Linien verwendet.
Die Verwendung von Druckluft ist beliebt, weil sie eine bequeme und sichere Energiequelle ist.
Aber viele vergessen, dass Druckluft eine der ineffizientesten Energiequellen ist – nur 5 % des Stroms, der für die Drucklufterzeugung aufgewendet wird, wird zu nützlicher Arbeit, die restlichen 95 % gehen in die Rohrleitung.
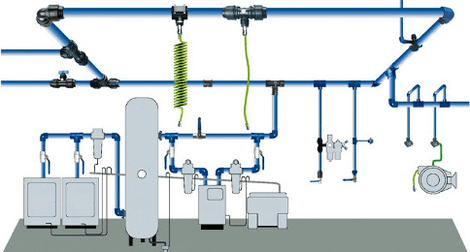
Energiesparen im Betrieb - Druckluft:
- Verwenden Sie keine Druckluft, um die Räumlichkeiten zu reinigen.
- Eine Reduzierung der Lufttemperatur am Kompressoreingang um 3 % reduziert den Stromverbrauch um 1 %.
- Reduzieren Sie bei diesen technischen Prozessen den Druckluftdruck nach Möglichkeit auf ein Minimum. Eine Reduzierung des Drucks um 10 % reduziert den Stromverbrauch um 5 %.
- Führen Sie regelmäßige Inspektionen, Reparaturen von Kompressoranlagen und Druckluftleitungen durch. Eine, selbst die kleinste Leckage von Druckluft, kann manchmal die Effizienz der Ausrüstung verringern.

Energiesparen im Betrieb – wir reduzieren Wärme- und Dampfverluste
Dampf wird häufig in der Industrie verwendet, insbesondere in der Textil-, Lebensmittel- und Verarbeitungsindustrie.
Durch die Verbesserung der Effizienz von Dampfkesseln und die Wiederverwendung der erzeugten Wärme kann der Energieverbrauch in diesen Anlagen deutlich gesenkt werden.
Dampfproduktion
Der Kessel arbeitet am effizientesten bei voller Leistung.
Aufgrund der Tatsache, dass sich der Bedarf an Dampfmenge im Laufe der Zeit ändern kann, kommt es häufig vor, dass der Kessel unter seiner optimalen Last arbeitet.
Die Kapazität des installierten Kessels kann aufgrund eines Rückgangs der Produktnachfrage oder nicht realisierter Pläne zur Erweiterung der Produktion viel höher sein als der Bedarf des Unternehmens.
Außerdem kann die Kesselkapazität aufgrund von Verbesserungen im Produktionsprozess oder der Einführung von Energiesparmaßnahmen nicht benötigt werden.
In solchen Fällen arbeitet der Kessel entweder nicht mit voller Leistung oder im Modus kurzer Ein-Aus-Zyklen.
Beide Situationen bringen erhebliche Energieverluste mit sich.
Es gibt keine einfachen und billigen Lösungen für dieses Problem.
Die einfachste Möglichkeit istInstallieren Sie einen "kleinen" Kessel, der mit voller Leistung funktioniertbei durchschnittlicher oder geringer Auslastung im Unternehmen.
Obwohl dies keine billige Lösung ist, kann die Amortisationszeit für eine solche Investition weniger als zwei Jahre betragen.
Und im Allgemeinen ist es immer effizienter, mehrere kleine austauschbare Kessel zu haben, insbesondere in Unternehmen mit wechselndem Bedarf oder starken saisonalen Schwankungen des Wärme- und Dampfverbrauchs.
Automatisches Regulierungssystem
Wenn das Unternehmen über mehrere Kessel verfügt, ist die Installation sinnvollautomatisches System zur Regulierung der Kessellast. . .
Die Automatisierung reagiert auf den Dampfbedarf im Unternehmen, verteilt die Last zwischen den Kesseln, schaltet die Kessel ein oder aus und erhöht so die Effizienz des gesamten Systems erheblich.
Absperrschieber
In Betrieben, in denen regelmäßig Kessel wegen sinkender Dampfnachfrage abgeschaltet werden, können die Wärmeverluste durch den Schornstein recht hoch sein.
Es ist möglich, den Heißluftverlust durch den Schornstein zu blockierendurch Einbau eines Absperrschiebersdie das Rohr verschließt, wenn der Kessel ausgeschaltet wird.
Prävention und Wartung
Wenn sie unbeaufsichtigt bleiben, können Brenner und Kondensatrückführungssysteme schnell verschlechtern oder ausfallen.
Dies kann den Wirkungsgrad des Kessels um 20 bis 30 % reduzieren.
Ein einfaches Wartungsprogramm, das sicherstellt, dass alle Kesselkomponenten auf maximalem Niveau arbeiten, erhöht die Betriebseffizienz erheblich.
In der Praxis reduziert eine regelmäßige Wartung den Energieverbrauch des Kessels um 10 %.
Isolierung - Der Wärmeverlust von der Oberfläche eines ordnungsgemäß isolierten Kessels sollte unter 1% liegen.
Entfernung von Ruß und Zunder
Es ist notwendig, die Rußbildung an den Kesselrohren und den Kesselstein ständig zu überwachen und zu beseitigen.
Eine 0, 8 Millimeter dicke Rußschicht reduziert die Wärmeübertragung um 9, 5%, während eine 4, 5 Millimeter dicke Schicht die Wärmeübertragung um 69% reduziert!
Kesselstein bildet sich, wenn sich Kalzium, Magnesium und Silizium auf dem Wärmetauscher des Kessels ablagern.
1 Millimeter dicke Skala erhöht den Energieverbrauch um 2 %.
Ruß und Zunder können mechanisch oder mit Säuren entfernt werden.
Die Bildung von Ruß und Kesselstein kann durch Temperaturerhöhung der Abgase oder durch Sichtkontrolle bei Nichtbetrieb des Kessels festgestellt werden.
Die Ruß- und Kesselsteinbildung muss besonders sorgfältig überwacht werden, wenn der Kessel mit festen Brennstoffen (Kohle, Torf, Brennholz) betrieben wird.
Gaskessel sind weniger anfällig für Rußprobleme.
Boiler-Blowdown-Optimierung
Kesselabschlämmung ist das Ablassen von Kesselwasser, um das Wasser im Kessel von Verunreinigungen und Salzen zu reinigen.
Der Zweck der Kesselabschlämmung besteht darin, die Bildung von Kesselstein zu vermeiden oder zu reduzieren.
Eine ungenügende Kesselabschlämmung kann dazu führen, dass Wasser in den Dampf gelangt oder sich Ablagerungen im Kessel bilden.
Übermäßiges Abblasen bedeutet Verlust von Wärme, Wasser und Chemikalien.
Die optimale Abschlämmstufe hängt vom Kesseltyp, dem Betriebsdruck im Kessel, der Aufbereitung und Qualität des verwendeten Wassers ab.
Das erste, worauf Sie achten sollten, ist die Wasseraufbereitung. Bei gut aufbereitetem Wasser (geringer Salzgehalt) kann die Abschlämmrate 4% betragen.
Bei Fremdkörpern und Salzen im Wasser beträgt die Abschlämmrate 8% -10%.
Auch der Energieverbrauch kann durch das automatische Absalzsystem deutlich gesenkt werden.
Die Amortisationszeit für ein solches System beträgt in der Regel 1-3 Jahre.
Reduzierung der Rauchemissionen
Übermäßiger Rauch entsteht häufig durch das Eindringen von Luft in Kessel und Schornstein durch Undichtigkeiten und Öffnungen.
Dies reduziert die Wärmeübertragung und erhöht die Belastung des Kompressorsystems.
Undichtigkeiten und Löcher können leicht beseitigt werden, es ist lediglich eine periodische Sichtkontrolle des Kessels und des Schornsteins erforderlich.
Luftregulierung
Je mehr Luft zum Verbrennen von Kraftstoff verwendet wird, desto mehr Wärme wird in den Wind geworfen.
Eine Luftmenge, die leicht über dem idealen stöchiometrischen Kraftstoff/Luft-Verhältnis liegt, ist aus Sicherheitsgründen zur Reduzierung der NOx-Emissionen erforderlich und hängt von der Kraftstoffart ab.
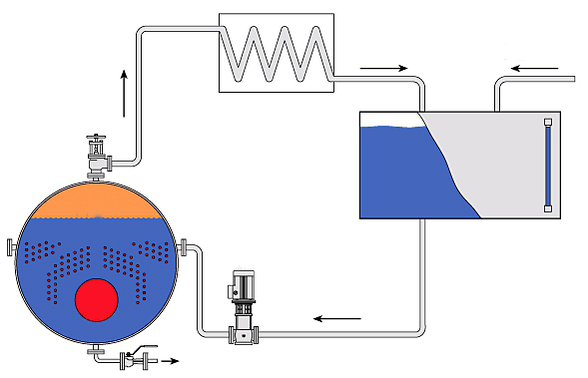
Kessel in schlechtem technischen Zustand können bis zu 140 % zusätzliche Luft verbrauchen, was zu übermäßigen Abgasemissionen führt.
Ein effizienter Gasbrenner benötigt 2 bis 3 % zusätzlichen Sauerstoff oder 10 bis 15 % zusätzliche Luft, um den Brennstoff zu verbrennen, ohne Kohlenmonoxid zu erzeugen.
Als Faustregel gilt, dass sich der Kesselwirkungsgrad um 1 % pro 15 % weniger zusätzlicher Luft erhöht.
Daher ist es notwendig, das Kraftstoff-Luft-Verhältnis ständig zu überprüfen.
Diese Veranstaltung kostet nichts, hat aber eine sehr gute Wirkung.
Überwachung der Rauchentwicklung
Die Sauerstoffmenge im Rauchgas ist die Summe aus zusätzlicher Luft (zur Erhöhung der Sicherheit und Reduzierung von Emissionen) und Luft, die durch Löcher und Undichtigkeiten in den Kessel eindringt.
Das Vorhandensein von Undichtigkeiten und Löchern kann leicht erkannt werden, wenn ein Überwachungssystem für die einströmende Luft und den Sauerstoffgehalt in den Rauchgasen eingerichtet wird.
Anhand der Daten zur Kohlenmonoxid- und Sauerstoffmenge ist es möglich, das Brennstoff-Luft-Verhältnis im Kessel zu optimieren.
Die Installation eines Überwachungs- und Analysesystems für Abgasemissionen amortisiert sich in der Regel in weniger als einem Jahr.
Energiesparen im Unternehmen – Installation eines Economizers
Die Wärme der Rauchgase kann genutzt werden, um das in den Kessel eintretende Wasser zu erwärmen.
Das erhitzte Wasser gelangt in den Kessel und benötigt weniger Wärme, um in Dampf umgewandelt zu werden, wodurch Brennstoff gespart wird.
Der Wirkungsgrad des Kessels erhöht sich um 1% pro 22°C Abnahme der Abgastemperatur.
Der Economizer kann den Kraftstoffverbrauch um 5% - 10% reduzieren und wird sich in weniger als 2 Jahren amortisieren.
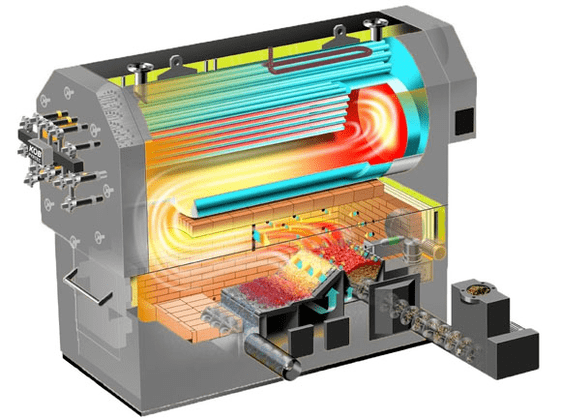
Wärmetauscher zur Wärmegewinnung aus Wasser und Dampf aus der Kesselabschlämmung
Der Wärmetauscher hilft dabei, etwa 80 % der Wasser- und Dampfwärme aus der Kesselabschlämmung zu recyceln.
Diese Wärme kann verwendet werden, um Gebäude zu heizen oder das Wasser zu erhitzen, das den Kessel speist.
Jeder Kessel mit einer konstanten Abschlämmrate von 5 % oder mehr ist ein ausgezeichneter Kandidat für einen Wärmetauscher.
Wenn das Absalzsystem nicht in einem konstanten Modus arbeitet, ist es sinnvoll, darüber nachzudenken, es in einen konstanten Modus zu überführen und gleichzeitig einen Wärmetauscher zu installieren.
Die durchschnittliche Amortisationszeit eines Wärmetauschers wird 1, 5 - 2 Jahre nicht überschreiten.
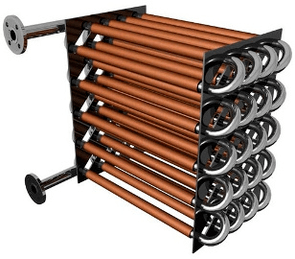
Installation eines Kondensations-Economizers
Heißes Kondensat kann in den Kessel zurückgeführt werden, wodurch Energie gespart und der Bedarf an aufbereitetem Wasser reduziert wird.
Der kondensierende Economizer kann die Effizienz der Anlage um weitere 10 % steigern.
Die Installation eines solchen Economisers sollte unter strenger Aufsicht von Spezialisten erfolgen, die alle Nuancen eines solchen Systems, seine Auswirkungen auf den Kessel und die chemische Zusammensetzung des Wassers berücksichtigen.
Die Verwendung eines Systems, das Kondensat zum Kessel zurückführt, amortisiert sich normalerweise in 1-1, 5 Jahren.
Ein System, das Kondensat zu einer Warmwasserversorgung leitet, amortisiert sich in weniger als einem Jahr.
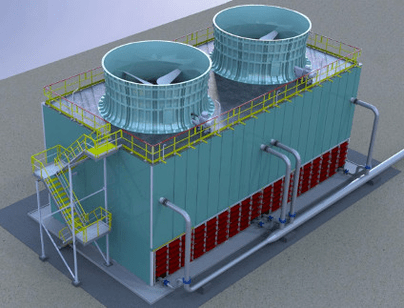
Kühltürme (Kühltürme)
Ein Kühlturm ist ein Wärmetauscher, in dem Wasser durch einen Luftstrom gekühlt wird.
Und in Bezug auf die Energieeffizienz ist ein Kühlturm ein Gerät, das Wärme an den Wind abgibt.
Energieeinsparpotenzial in Kühltürmen:
- In manchen Betrieben ist es sinnvoll, ganz auf Kühltürme zu verzichten. Es gibt viele Fälle, in denen eine Heizung zum Heizen eines Raumes verwendet wird und gleichzeitig ein Kühlturm zur Wärmeabfuhr verwendet wird. Die Installation einer Wärmepumpe löst das Heizungsproblem und reduziert zumindest teilweise die Notwendigkeit, den Kühlturm zu verwenden.
- Durch die Installation von Leistungsschaltern für Kühlturmlüfter kann der Energieverbrauch um 40 % gesenkt werden.
- Der Austausch von Aluminium- oder Eisenlüftern durch neue Lüfter (Glasfaser- und Kunststoffguss) kann den Energieverbrauch um bis zu 30 % senken.
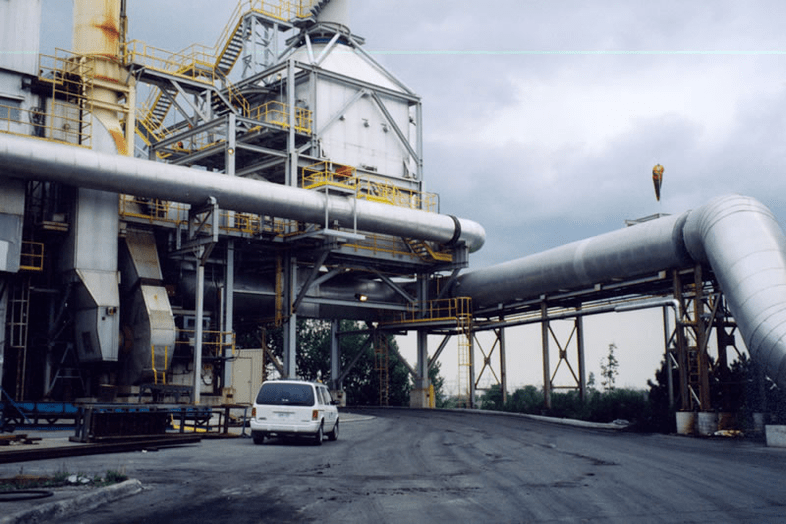
Reduzierung von Verlusten in Dampfleitungen
Trennen nicht beanspruchter Dampfleitungen
Dampfbedarf und -verbrauch ändern sich ständig.
Dies kann dazu führen, dass nicht das gesamte Dampfverteilsystem voll ausgelastet wird, sondern nur 20 % -50 %, was unweigerlich zu Wärmeverlusten führt.
Es ist klar, dass die Optimierung oder Neukonfiguration des gesamten Dampfverteilungssystems zur Erfüllung neuer Anforderungen sehr teuer und möglicherweise nicht durchführbar ist.
Das Erkennen und Abschalten von Dampfleitungen, die kaum genutzt werden, kann jedoch eine sehr effektive Energiesparmaßnahme sein.
Energiesparen im Unternehmen - Wärmedämmung von Rohren
Das Isolieren von Dampfrohren kann Energieverluste um bis zu 90 % reduzieren.
Dies ist eine der schnellsten Energieeinsparungen in einem Dampfverteilungssystem.
Die durchschnittliche Amortisationszeit für die Isolierung von Rohrleitungen, durch die Dampf oder Heißwasser geleitet wird, beträgt etwa 1 Jahr.
Kondensatleitungen für 1, 5-2 Jahre.
Überwachung von Kondensatableitern
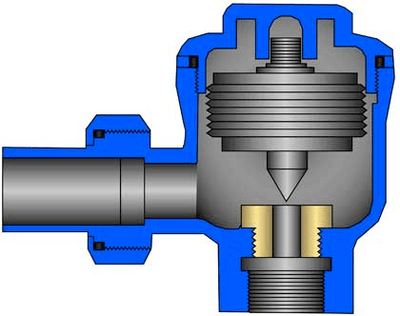
Ein einfaches Überwachungsprogramm für den technischen Zustand von Kondensatableitern kann den Wärmeverlust deutlich reduzieren.
Wenn beispielsweise 3 bis 5 Jahre keine Wartung durchgeführt wurde, ist in der Regel etwa ein Drittel der Kondensatableiter defekt, wodurch Dampf in das Kondensatableitersystem eindringen kann.
Aus der Praxis sind in Betrieben, die über ein Überwachungsprogramm für Kondensatableiter verfügen, nicht mehr als 5 % der Kondensatableiter in einem fehlerhaften Zustand.
Die durchschnittliche Amortisationszeit für den Austausch oder die Wartung eines Kondensatableiters beträgt weniger als sechs Monate.
Ein Überwachungsprogramm für Kondensatableiter reduziert typischerweise die Dampfverluste um 10 %.
Thermostatische Kondensatableiter
Der Einsatz moderner Thermostat-Kondensatableiter kann den Energieverbrauch senken und gleichzeitig die Zuverlässigkeit des Gesamtsystems erhöhen.
Der Hauptvorteil von Thermostat-Kondensatableitern ist, dass sie
- geöffnet, wenn sich die Temperatur dem Sattdampfniveau nähert (+/- 2 C °),
- nach jedem Öffnen nicht kondensierbare Gase abgeben und
- befinden sich zu Beginn des Systembetriebs im geöffneten Zustand, was eine schnelle Erwärmung gewährleistet.
Außerdem sind diese Kondensatableiter sehr zuverlässig und können in einem weiten Druckbereich eingesetzt werden.
Kondensatableiter trennen
Sie können den Energieverbrauch reduzieren, indem Sie Kondensatableiter an den Heißdampfleitungen bei Nichtgebrauch abschalten.
Beseitigung von Dampflecks
Ein Programm zur Reparatur von Dampflecks bei kleinen Löchern kann sich in weniger als 3 bis 4 Monaten auszahlen.
Wir dürfen nicht vergessen, dass kleine Lecks jahrelang unbemerkt bleiben und das System ständig beschädigen können.
Wiederverwendung von Kondensat und Dampf
Wenn ein Kondensatableiter Kondensat aus einem Dampfsystem ableitet, erzeugt der Druckabfall Dampf aus diesem Kondensat.
Dieser Dampf kann zusammen mit Kondensat in einem Wärmetauscher zur Erwärmung von Speisewasser oder Luft verwendet werden.
Vor allem ist es möglich, diesen Dampf und das Kondensat in der Nähe der Austrittsstelle zu verwenden, da es sehr kostspielig sein kann, ein separates Rohrleitungssystem zu schaffen, um es zur Verwendungsstelle zu transportieren.